Hydraulic systems provide powerful actuation for all kinds of industrial machinery and vehicles. At the heart of these systems are hydraulic cylinders, which convert fluid pressure into straight-line motion or force. Small double acting hydraulic cylinders in particular play an important role due to their compact size yet ability to perform bidirectional movement. This blog post will explore the key engineering aspects of these specialized cylinders.
What is a Double Acting Hydraulic Cylinder?
A double acting cylinder contains two ports that allow hydraulic fluid to alternately pressurize either side of the piston, enabling extension and retraction in a single cylinder body. This bidirectional actuation allows components to move in two directions, unlike single acting cylinders which only push or pull on the extension stroke. Double acting cylinders provide 180-degree motion cycles rather than the 90-degree strokes from two singles.
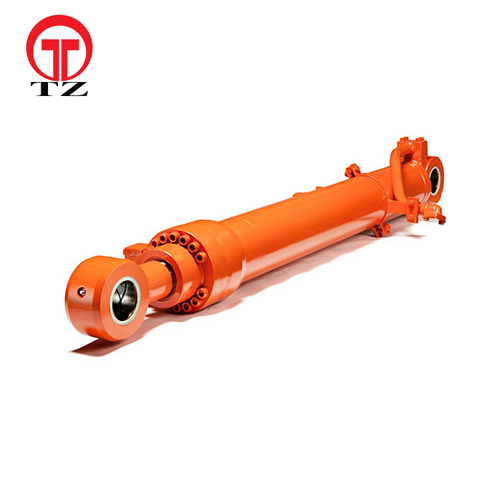
Typical Applications
Small double acting cylinders below 5 inches in diameter commonly find roles in applications like:
Scissor lifts and lifts tables for height adjustment
Mud flaps and spoiler actuation in vehicles
Industrial graspers, clamps and pinchers
Construction equipment attachments
Medical equipment articulation
Robotics joints and positioning
Their compact nature allows installation into tight spaces while generating considerable forces from just millimeters of stroke.
Design and Operation
At the heart of the cylinder is a solid steel piston driven by pressurized hydraulic fluid. Precise tolerances and polished surfaces allow minimal leakage past seals. The cylinder tube is constructed of hardened steel or aluminum alloy for durability. Ports located at rod and rodless ends allow independent pressurization on either side of the piston through supply lines. Internal ducts route fluid, with counterbalance valves controlling flow direction.
During extension, fluid pressure from the pump passes through one port to advance the rod. Retraction occurs as fluid exits this port and enters the opposing port behind the piston. Rod mounting ends and protective shrouds complete package configurations. Internal components include seals, bearings and seals to minimize friction during cycling.
Performance Characteristics
Key specifications of small double acting cylinders include stroke length, bore diameter determining force output, and maximum operating pressures up to 5000 PSI. Extended service life depends on factors like cycle rate count, rod carriage design, seals used and cleanliness of hydraulic fluid. Speed of actuation varies considerably based on pump flow rates matched to cylinder sizing. Forces produced range from just a few pounds up to several tons for larger bore sizes.
Sizing Considerations
To select the properly sized cylinder, it’s important to calculate the forces or pressures needed to be overcome. Stroke needs plus space envelopes constrain minimum cylinder dimensions. Attention must also be paid to mounting lugs and rod ends, fluid connections, and any required mounting brackets or adapters. Testing sometimes needs simulating to confirm adequate performance without oversizing. Manufacturers provide application engineering support and catalog selections for common applications.
Maintenance and Reliability
Double acting hydraulic cylinders require minimal maintenance given their simple design, but certain factors influence long term reliability. Contamination control through high-quality filtration extends seal and bearing life. Strategic venting reduces cavitation concerns. Proper mounting with anti-rotation safeguards prevents premature fatigue failure. Thermal expansion effects should likewise be addressed in cylinder design. Periodic inspection allows replacement of seals and o-rings before failure occurs. Overall, quality manufacturing with tight tolerances paired with clean hydraulic fluid provides years of dependable service life.
In conclusion, small double acting hydraulic cylinders excel at providing bidirectional actuation where space is constrained. Their versatile functionality enables all kinds of industrial processes and equipment movement through intelligent hydraulic system design. Accounting properly for selection criteria ensures optimal performance and reliability long term.